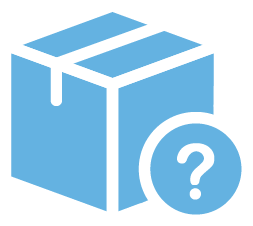
Need help choosing the right product?
Our tool will match the best product to your needs
Launch product selectorWelcome to the USA Website
We have detected that you may prefer the Global site. Please use the language dropdown above to change your selection if required.
Product Selector
Our tool will match the best product to your needs
Launch product selectorContact Us